Automated power management system increases safety aboard full-rigged ship
Automated power management system increases safety aboard full-rigged ship
One of the world’s oldest, civil training ship, Georg Stage has been undergoing a complete retrofit, including implementing a modern power management system. A system that improves the safety on board, automates synchronisation and saves the staff a lot of time.
Many locals are lined up at the dock to see the beautiful, old training ship Georg Stage that is moored in Svendborg port for a few days. The Danish flag flutters in a balmy breeze, and the three-masted fully rigged ship looks stunning with its polished brass and three 30m masts.
We are welcomed by Chief Engineer and former student at the self-same ship, Mathilde Romer Olsen, who is responsible for making the engine room machinery work appropriately for a smooth voyage and for training the deck hands in machinery. Georg Stage attracts attention wherever it comes, and the ship is often open for visitors. This day, a group of school children gets a guided tour by one of the students who with great enthusiasm, explains the group what it is like living on board the ship.
Georg stage is built in 1934 and provides young people with maritime education and experiences of a lifetime. Unlike other training ships, Georg Stage is not associated with any onshore school, and it is one of the oldest, civil training ship in the world. Every year, Georg Stage completes two 20-week expeditions, and the crew counts 10 employees and 63 students. The old vessel sails primarily in the North European waters and is right now in Denmark where it will complete its current expedition that started in Alicante, Spain back in February.
The training ship is beautiful, but it has taken a comprehensive retrofit to appear like this.
Being along in years, Georg Stage needed to be shined up, and in 2017, Assens Shipyard began a complete retrofit that lasted for nine months and comprised all parts of the ship.
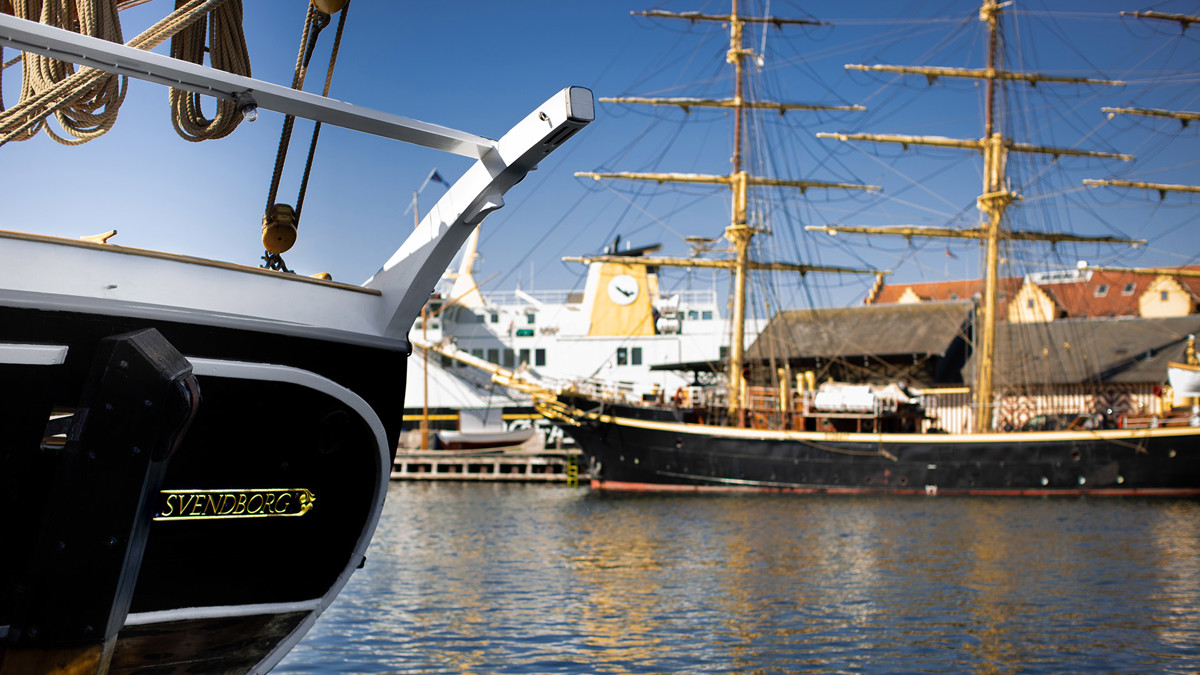
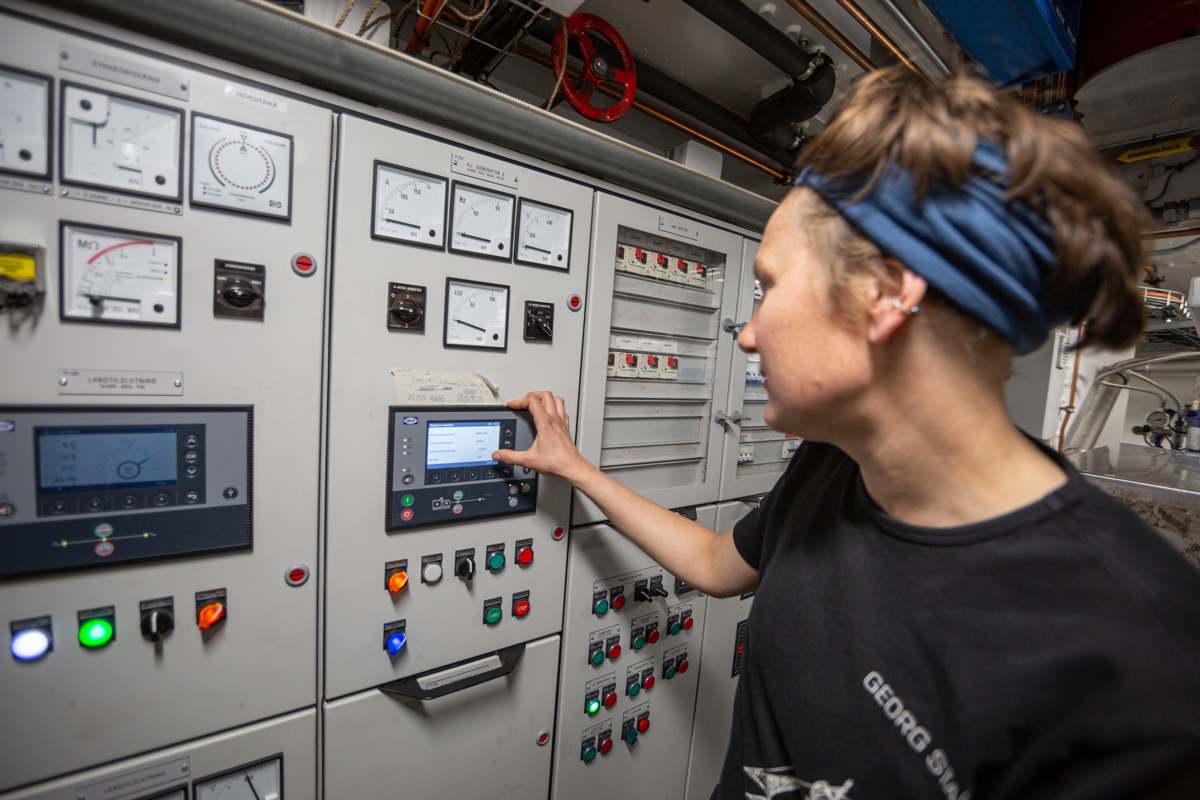
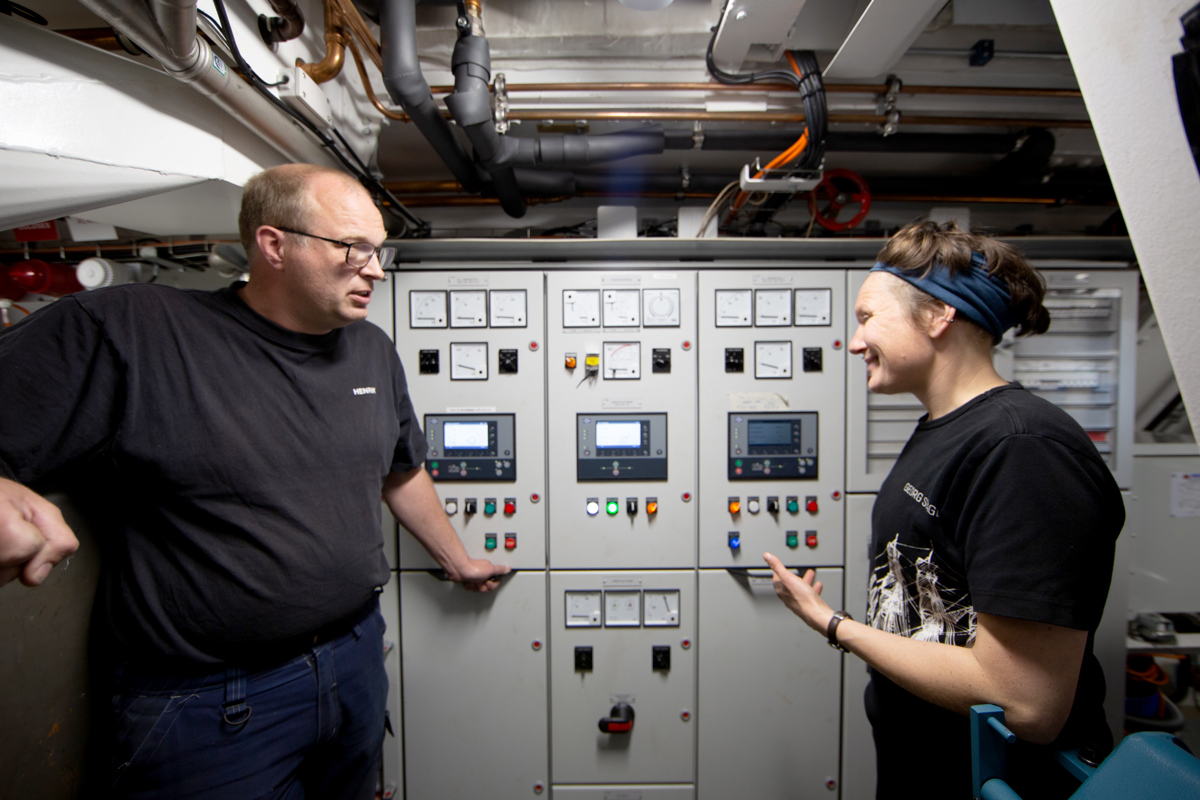
New power management system saves time and space
Besides a lot of new steelwork, the retrofit also included initiatives that would modernise everyday life on board and make it easier and more enjoyable for the crew. But the new initiatives also increased the requirements for the power management system. “The more electrical equipment we implement on board, the more dependent we are on having a stable and efficient power supply”, Mathilde explains.
As part of the extensive refit, the engine room was completely rebuilt and upgraded. Something that was much needed since it was worn and obsolete, Mathilde explains.
Only the main engine and the two auxiliaries were retained; everything else was replaced, including a new, automated power management system to prevent blackout situations and to smooth everyday operations.
“Before we manually synchronised the engine and we also set the load sharing manually. If an auxiliary stopped running, we had a blackout situation, and we had to manually start up the second auxiliary and restart everything – a situation that we often experienced”, says Mathilde. Also, it was important that the new solution would take up as little space as possible. “When you only have very little space available, every centimetre counts”, the chief engineer says with a smile.
The naval electro service contractor, Koelco ApS, was asked to design a space-saving solution comprising a new shore connection. “Previous there was a separate switchboard, and then a control panel for each of the two auxiliaries, but with only a very little space available, we decided to build one main switchboard comprising the power management system that also controls of the auxiliaries”, explains Henrik Skøtt-Christensen, owner of Koelco ApS. As some DEIF equipment already was installed, it was decided to base the solution on DEIF’s versatile PPM 300 controller.
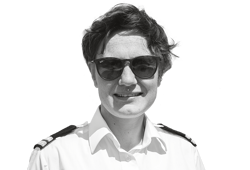
“The new system makes my job much easier. The synchronisation is done automatically in a split second, and we no longer need to restart everything when connecting to onshore power”
Mathilde Romer Olsen
Chief Engineer, Georg Stage
Intuitive system improves safety
Creating a solution that would meet all requirements caused trouble for both the chief engineer and the electrical contractor, and Henrik admits that designing the system has caused him sleepless nights, and a lot of phone calls between Mathilde and him. In the end, their struggles paid off, and the new power management system onboard Georg Stage lives up to expectations.
“The new system makes my job much easier. The synchronisation is done automatically in a split second, and we no longer need to restart everything when connecting to onshore power”, Mathilde says.
All in all, the new power management system improves safety on board, and it saves the chief engineer time and provides her with higher flexibility. “With the new system, we now have a reliable power supply. For example, when we are in port, I know that the system will start up in case of a power failure and it provides me with more flexibility when being ashore”, the chief engineer says.
After completing the installation, Henrik gave a brief introduction to the new system, which Mathilde finds intuitive to operate. A system that she can monitor from her cabin, where an AGI 415 touch screen displays what is going on in the engine room.
The training ship docks various places around the world, and quite often a shore-side power failure has left the ship in a blackout situation. The new power management system ensures that such situation no longer occurs. “If the shore-side power fails, the system automatically starts a generator, and we save both inconvenience and time on restarting everything. With the new system, people do not notice that we connect to the shore side power”, Mathilde concludes.
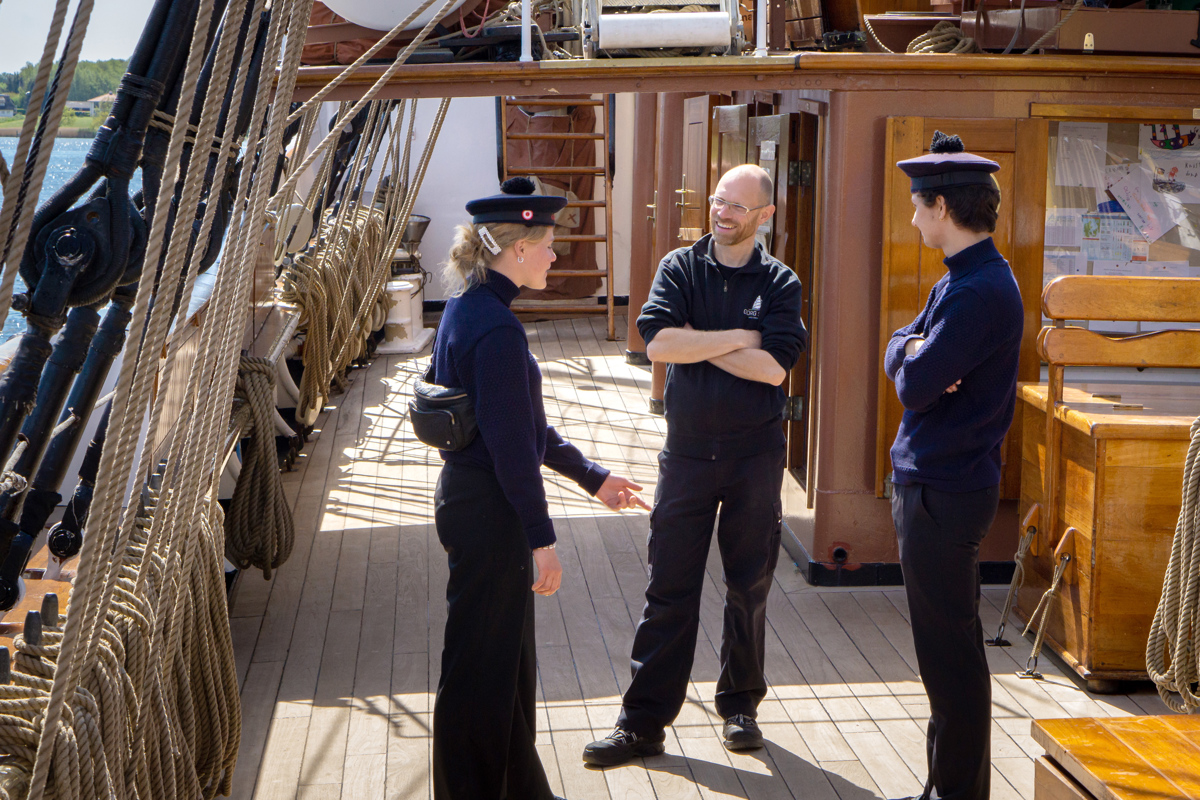
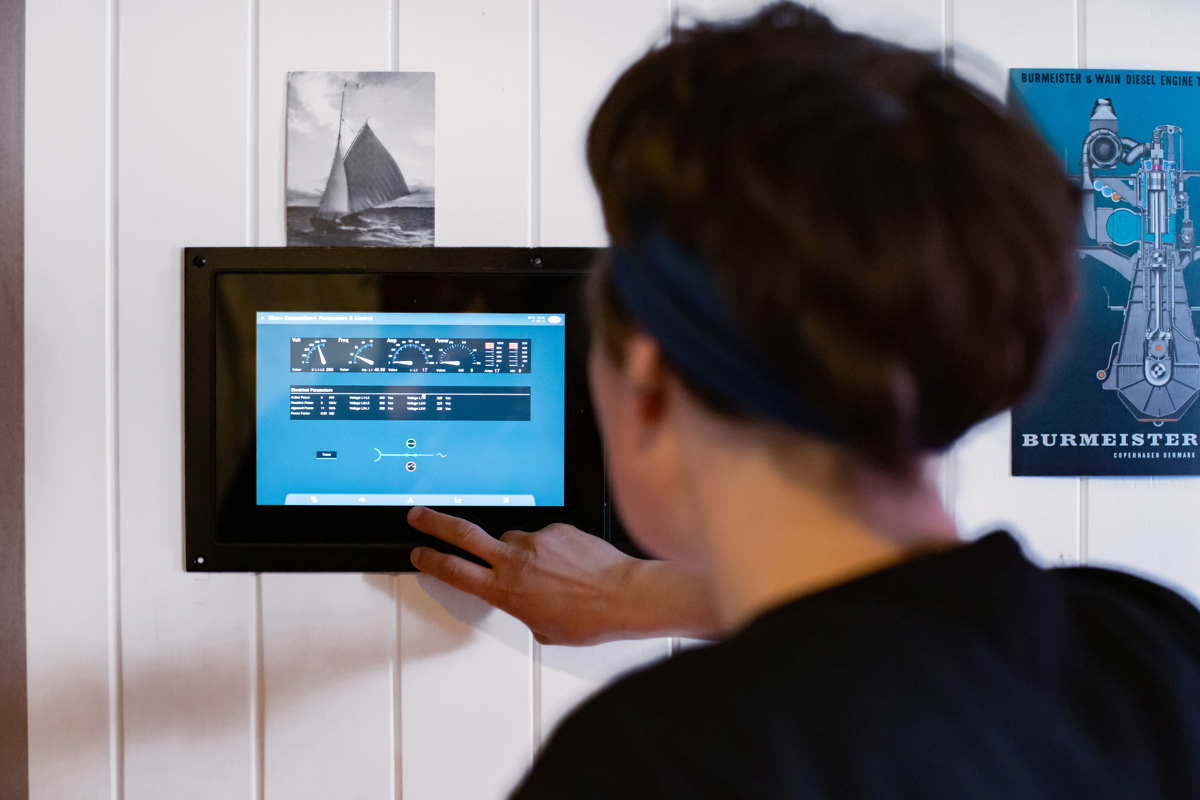
-
Contact us to discuss your options
- 90 years of energy pioneering
- Manufactured at the highest standards
- Superior quality
- Unmatched service and support
- Made in Denmark